Das Pultrusionsverfahren ist ein kontinuierliches Formverfahren, bei dem die mit Klebstoff imprägnierte Kohlefaser während des Aushärtens durch die Form geführt wird. Dieses Verfahren wurde bereits zur Herstellung von Produkten mit komplexen Querschnittsformen eingesetzt und hat sich daher als für die Massenproduktion und eine verbesserte Produktionseffizienz geeignetes Verfahren etabliert. Seine Anwendung nimmt zu. Allerdings treten während des Pultrusionsprozesses häufig Probleme wie Abblättern, Risse, Blasenbildung und Farbunterschiede auf der Produktoberfläche auf.
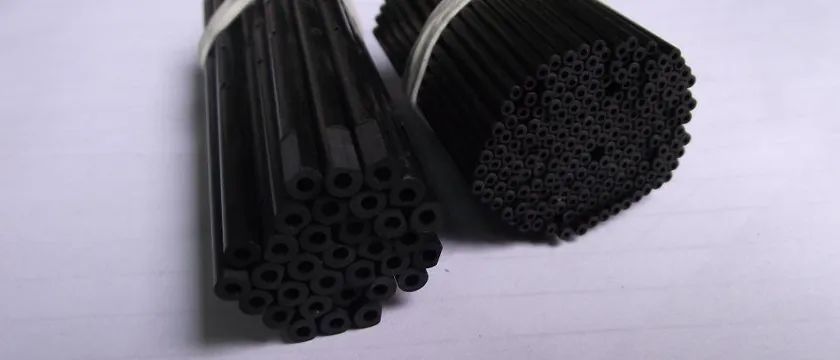
Abblättern
Wenn Partikel aus gehärtetem Harz aus der Form auf die Oberfläche des Teils gelangen, wird dieses Phänomen als Abblättern oder Abplatzen bezeichnet.
Lösung:
1. Erhöhen Sie die Temperatur am Einlassende der frühen Form des ausgehärteten Harzes.
2. Reduzieren Sie die Liniengeschwindigkeit, damit das Harz früher aushärtet.
3. Leitung zum Reinigen anhalten (30 bis 60 Sekunden).
4. Erhöhen Sie die Konzentration des Niedertemperaturinitiators.
Blase
Wenn auf der Oberfläche des Teils Blasenbildung auftritt.
Lösung:
1. Erhöhen Sie die Temperatur der Einlassendform, damit das Harz schneller aushärtet
2. Reduzieren Sie die Leitungsgeschwindigkeit, was den gleichen Effekt hat wie die oben genannten Maßnahmen
3. Erhöhen Sie den Verstärkungsgrad. Schaumbildung wird häufig durch Hohlräume verursacht, die durch einen niedrigen Glasfasergehalt entstehen.
Oberflächenrisse
Oberflächenrisse entstehen durch übermäßiges Schrumpfen.
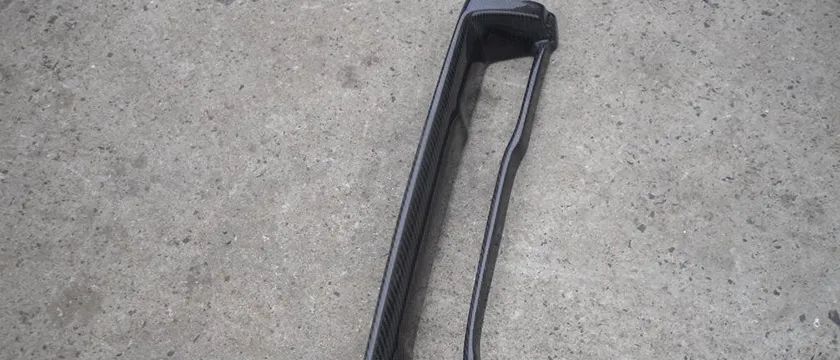
Lösung:
1. Erhöhen Sie die Formtemperatur, um die Aushärtungsgeschwindigkeit zu beschleunigen
2. Reduzieren Sie die Leitungsgeschwindigkeit, was den gleichen Effekt hat wie die oben genannten Maßnahmen
3. Erhöhen Sie den Füll- oder Glasfasergehalt des Füllstoffs, um die Zähigkeit der harzreichen Oberfläche zu erhöhen und dadurch Schrumpfung, Spannung und Risse zu reduzieren
4. Oberflächenpolster oder Schleier zu Teilen hinzufügen
5. Erhöhen Sie den Gehalt an Niedertemperaturinitiatoren oder verwenden Sie Initiatoren mit einer niedrigeren Temperatur als der aktuellen.
Innerer Riss
Innere Risse sind normalerweise auf einen übermäßig dicken Abschnitt zurückzuführen, und Risse können in der Mitte des Laminats oder an der Oberfläche auftreten.
Lösung:
1. Erhöhen Sie die Temperatur am Zufuhrende, um das Harz früher auszuhärten
2. Reduzieren Sie die Formtemperatur am Ende der Form und verwenden Sie sie als Kühlkörper, um den exothermen Peak zu reduzieren
3. Wenn die Formtemperatur nicht geändert werden kann, erhöhen Sie die Liniengeschwindigkeit, um die Temperatur der Außenkontur des Teils und den exothermen Peak zu senken und so die thermische Belastung zu verringern.
4. Reduzieren Sie den Anteil der Initiatoren, insbesondere der Hochtemperaturinitiatoren. Dies ist die beste dauerhafte Lösung, erfordert jedoch einige Experimente.
5. Ersetzen Sie den Hochtemperaturinitiator durch einen Initiator mit geringer Exothermie, aber besserer Härtungswirkung.
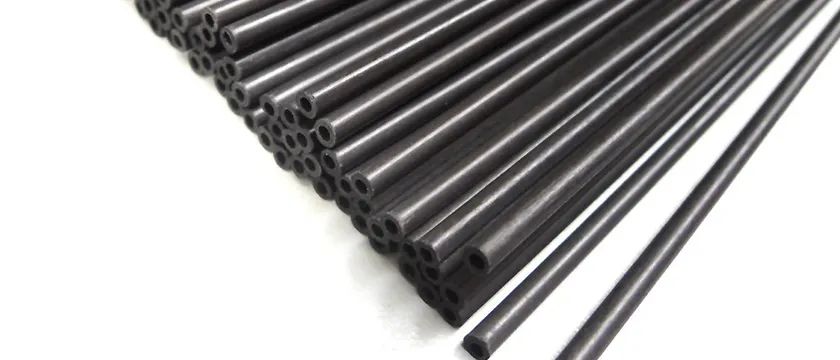
Chromatische Aberration
Hotspots können zu ungleichmäßiger Schrumpfung führen, was zu chromatischer Aberration (auch Farbübertragung genannt) führt.
Lösung:
1. Überprüfen Sie, ob die Heizung richtig sitzt, damit keine ungleichmäßige Temperatur auf dem Chip entsteht.
2. Überprüfen Sie die Harzmischung, um sicherzustellen, dass sich Füllstoffe und/oder Pigmente nicht absetzen oder trennen (Farbunterschied).
Geringe Bushärte
Geringe Barcol-Härte aufgrund unvollständiger Aushärtung.
Lösung:
1. Reduzieren Sie die Liniengeschwindigkeit, um die Aushärtung des Harzes zu beschleunigen
2. Erhöhen Sie die Formtemperatur, um die Aushärtungsrate und den Aushärtungsgrad in der Form zu verbessern
3. Achten Sie auf Mischungsformulierungen, die zu einer übermäßigen Plastifizierung führen
4. Prüfen Sie auf andere Verunreinigungen wie Wasser oder Pigmente, die die Aushärtungsrate beeinträchtigen können
Hinweis: Barcol-Härtewerte sollten nur zum Vergleich von Aushärtungen mit demselben Harz verwendet werden. Sie können nicht zum Vergleich von Aushärtungen mit unterschiedlichen Harzen verwendet werden, da unterschiedliche Harze mit ihren eigenen spezifischen Glykolen hergestellt werden und unterschiedliche Vernetzungstiefen aufweisen.
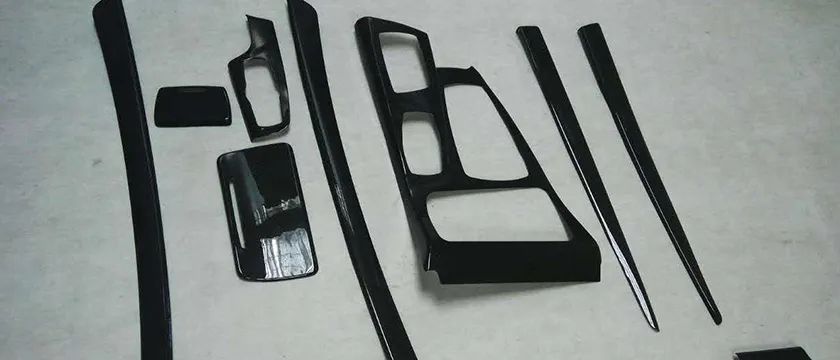
Luftblasen oder Poren
Auf der Oberfläche können Luftblasen oder Poren auftreten.
Lösung:
1. Prüfen Sie, ob beim Mischen oder durch unsachgemäßes Erhitzen überschüssiger Wasserdampf und Lösungsmittel entstehen. Wasser und Lösungsmittel sieden und verdampfen während des exothermen Prozesses, wodurch Blasen oder Poren auf der Oberfläche entstehen.
2. Reduzieren Sie die Liniengeschwindigkeit und/oder erhöhen Sie die Formtemperatur, um dieses Problem durch Erhöhen der Oberflächenhärte des Harzes besser zu lösen.
3. Verwenden Sie eine Oberflächenabdeckung oder einen Oberflächenfilz. Dies stärkt das Oberflächenharz und hilft, Luftblasen oder Poren zu beseitigen.
4. Fügen Sie den Teilen Oberflächenpolster oder Schleier hinzu.
Veröffentlichungszeit: 10. Juni 2022